Components
Automated welding station for circumferential tank welds
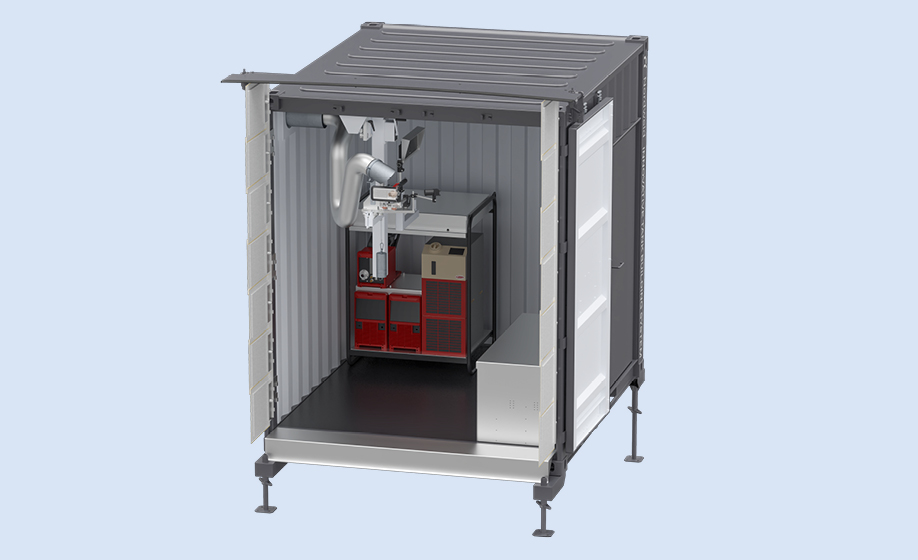
Automated welding station for circumferential tank welds
Dedicated welding container designed for performing high-quality circumferential welds on cylindrical tanks. All necessary welding components—including the power source, torch guiding system, control unit, and supporting accessories—are fully integrated within the container, ensuring mobility, quick deployment, and operational readiness.
Dedicated welding container designed for performing high-quality circumferential welds on cylindrical tanks. All necessary welding components—including the power source, torch guiding system, control unit, and supporting accessories—are fully integrated within the container, ensuring mobility, quick deployment, and operational readiness.
Welding Station for Plate Track
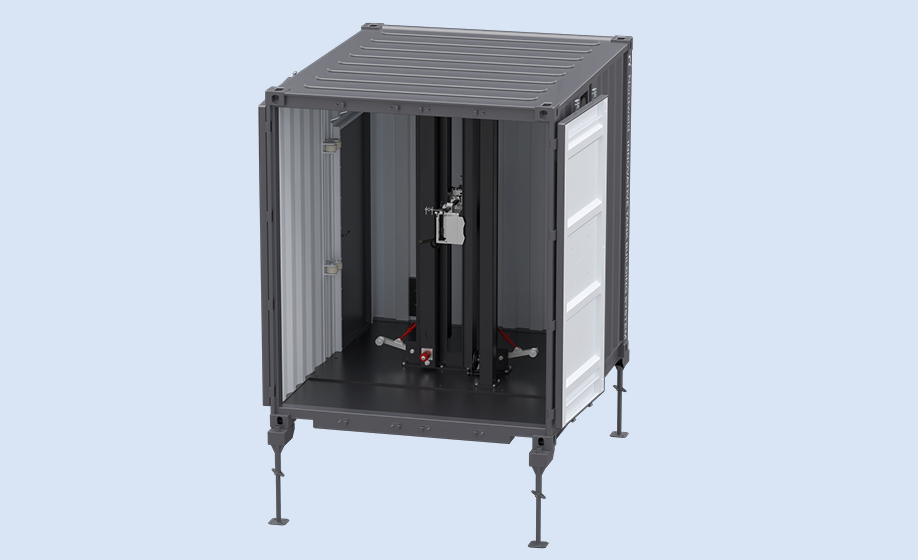
Welding Station for Plate Track
Automated container designed for the vertical assembly and welding of sheet metal plates. The system securely locks two sheets in a vertical position using hydraulic actuators, ensuring precise alignment before welding.
Automated container designed for the vertical assembly and welding of sheet metal plates. The system securely locks two sheets in a vertical position using hydraulic actuators, ensuring precise alignment before welding.
Lift Jack
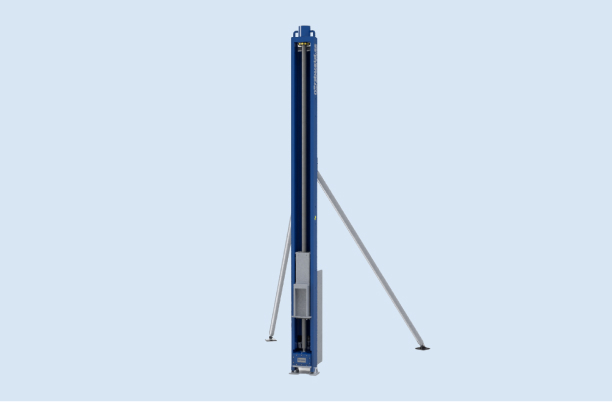
Lift Jack
Lift Jacks are used to erect tanks of larger diameter when building in a top-down method. Our electromechanical jacks have a lift height of 2100 mm (Lift Jack 9T) and 2600 mm (Lift Jack 15T). The supplied lift jack is CE marked and tested with 13.5 ton (Lift Jack 9T) and 25 ton (Lift Jack 15T), 50% dynamic load (+50%).
Lift Jacks are used to erect tanks of larger diameter when building in a top-down method. Our electromechanical jacks have a lift height of 2100 mm (Lift Jack 9T) and 2600 mm (Lift Jack 15T). The supplied lift jack is CE marked and tested with 13.5 ton (Lift Jack 9T) and 25 ton (Lift Jack 15T), 50% dynamic load (+50%).
Wheel Trolley
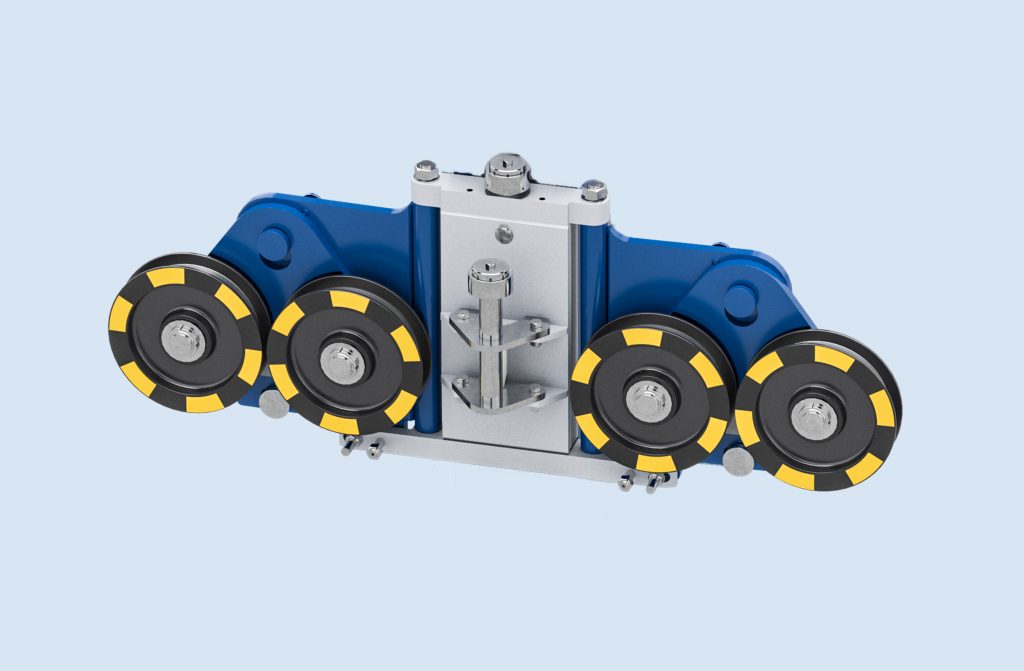
Wheel Trolley
The Wheel Trolley is a component of our Advanced System and is installed on the Lift Jack. The entire tank rolls on top of the Wheel Trolley. During the sheet feeding process, the trolleys are lowered individually from their elevated position (shell height) to the lower position using a dedicated high-speed button on the jacks.
The Wheel Trolley is a component of our Advanced System and is installed on the Lift Jack. The entire tank rolls on top of the Wheel Trolley. During the sheet feeding process, the trolleys are lowered individually from their elevated position (shell height) to the lower position using a dedicated high-speed button on the jacks.
Weld Gap Adjusting Jack
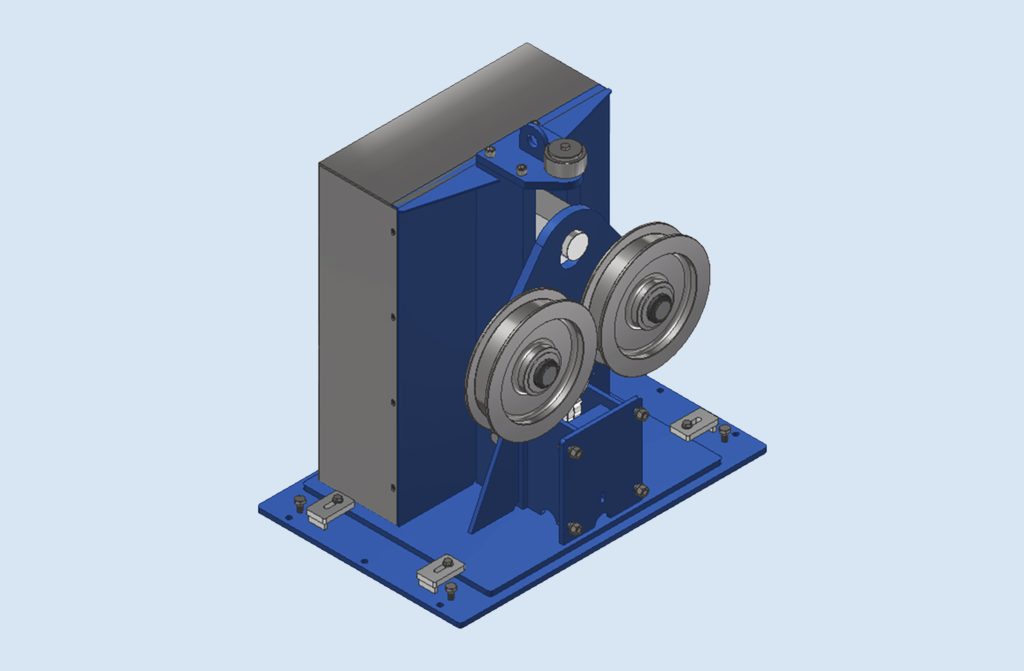
Weld Gap Adjusting Jack
Adjust the weld gap during sheet feeding from the bending machine using the weld gap adjusting jack. This jack, which features a 6,000 kg lifting capacity and a 75 mm lifting stroke, operates via remote control. It is used in our advanced system between the bending machine and the feeding point.
Adjust the weld gap during sheet feeding from the bending machine using the weld gap adjusting jack. This jack, which features a 6,000 kg lifting capacity and a 75 mm lifting stroke, operates via remote control. It is used in our advanced system between the bending machine and the feeding point.
Tank Rotator
Roller Bed
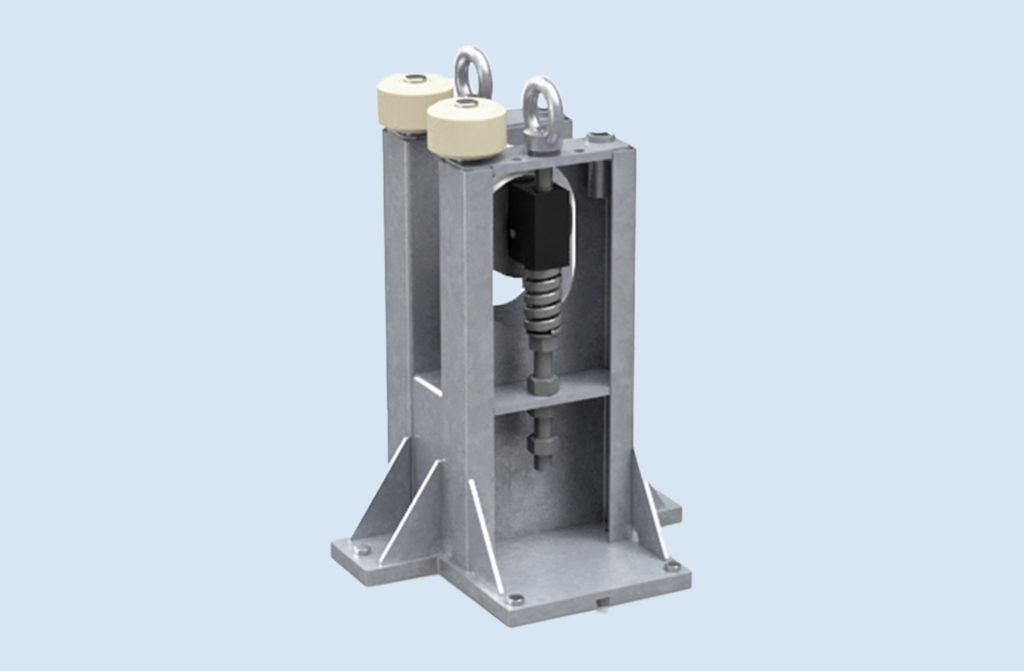
Roller Bed
The Roller Beds are positioned around the perimeter of the tank bottom. A flat bar ring is placed on the wheels of the roller beds to distribute the load of the entire tank. As the tank rolls, it moves along with the support ring. Additionally, a special scaffolding pipe can be attached to the roller beds, allowing for the installation of scaffolding consoles to create exterior or interior working platforms.
The Roller Beds are positioned around the perimeter of the tank bottom. A flat bar ring is placed on the wheels of the roller beds to distribute the load of the entire tank. As the tank rolls, it moves along with the support ring. Additionally, a special scaffolding pipe can be attached to the roller beds, allowing for the installation of scaffolding consoles to create exterior or interior working platforms.
Tack Weld Stand
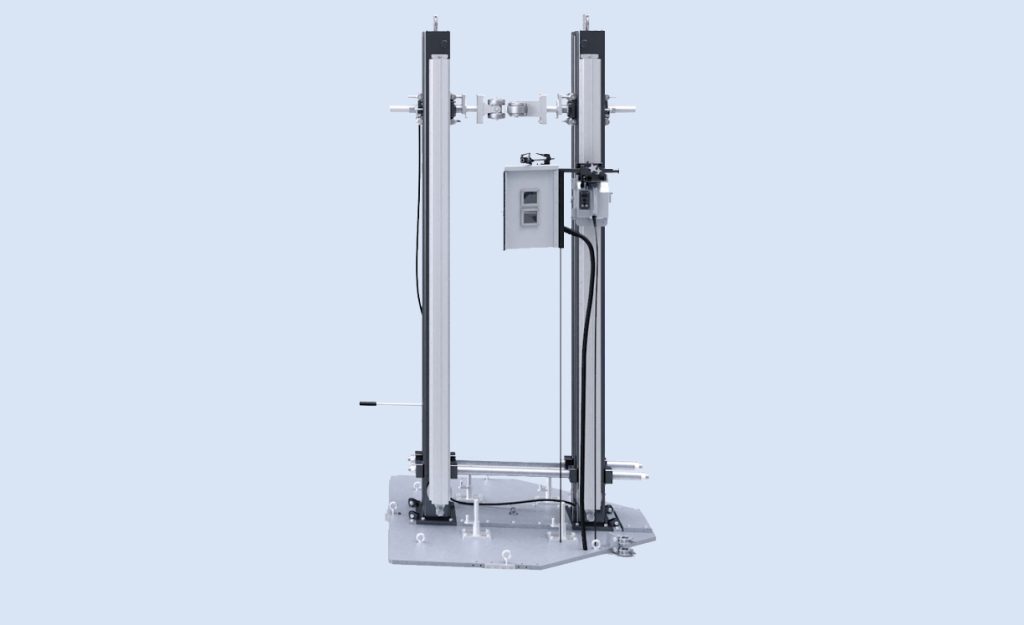
Tack Weld Stand
The horizontal joint is aligned as the tank rotates continuously. Tack welding is performed from a single location, making the process simple, fast, and cost-effective. When attaching stiffening rings to the tank wall, the stand can compress each ring segment securely against the tank wall.
The horizontal joint is aligned as the tank rotates continuously. Tack welding is performed from a single location, making the process simple, fast, and cost-effective. When attaching stiffening rings to the tank wall, the stand can compress each ring segment securely against the tank wall.
Weld Stand
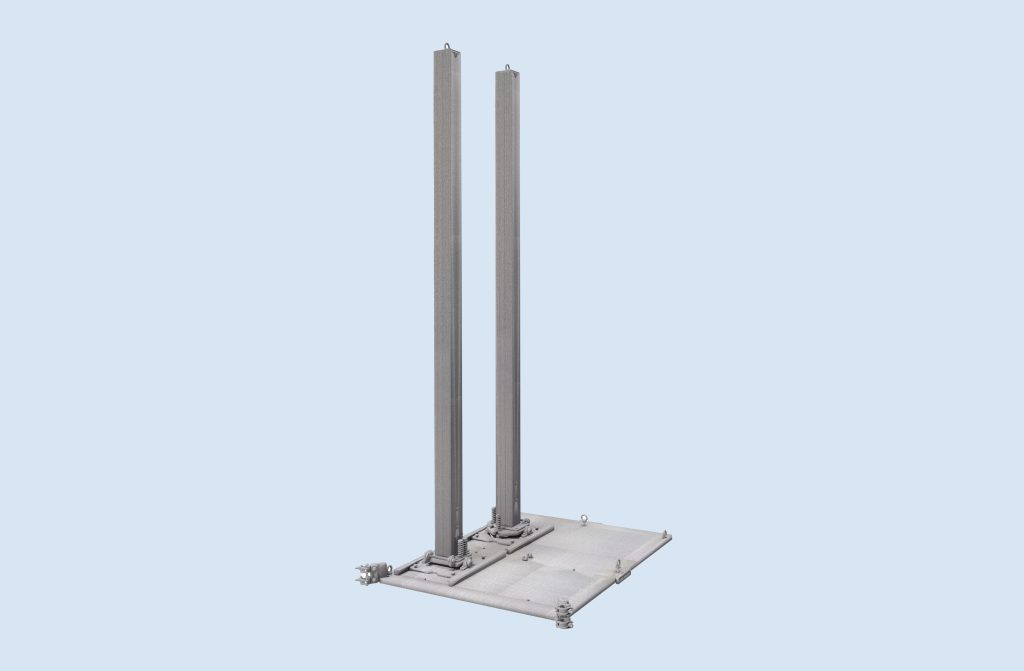
Weld Stand
The Weld Stand supports various mechanized welding applications, including MIG/MAG, SAW, Plasma, and Arc TIG. It features a base plate and two spring-loaded columns that continuously move inward toward the shell, ensuring stable and precise welding.
The Weld Stand supports various mechanized welding applications, including MIG/MAG, SAW, Plasma, and Arc TIG. It features a base plate and two spring-loaded columns that continuously move inward toward the shell, ensuring stable and precise welding.
Vertical Plate Bending Machine + Decoiler
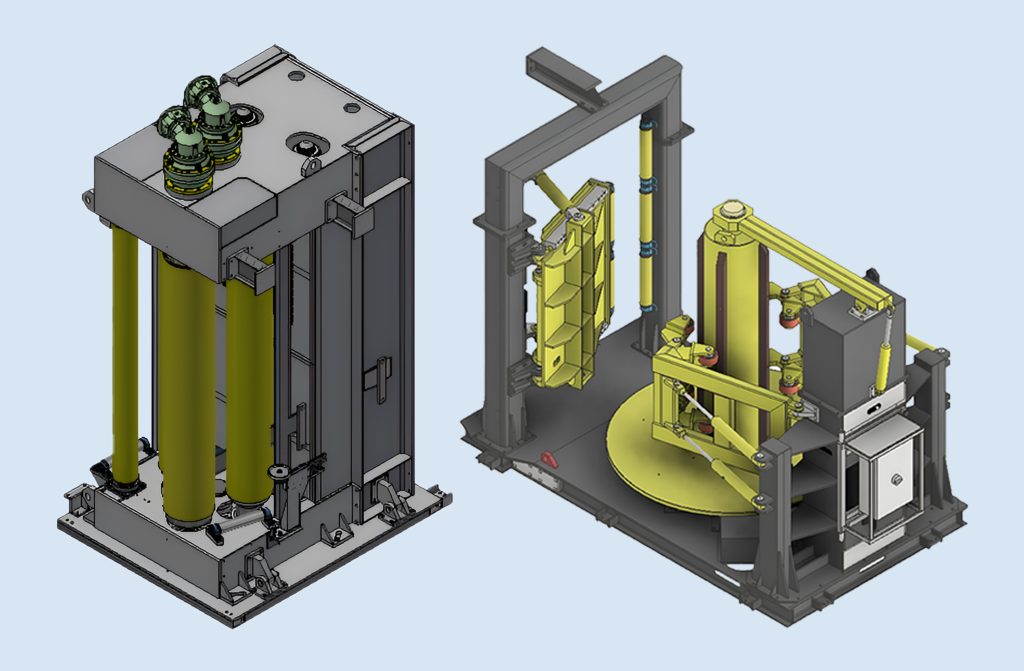
Vertical Plate Bending Machine + Decoiler
The vertical plate bending machine is designed for rolling straight plates or material from coils. It can be equipped with either 3, 4, or 7 rolls, and can be customized to accommodate different plate heights and thicknesses. The rolls are covered with urethane to prevent contamination of the rolled material. The machine is connected to a de-coiler for processing material directly from coils, which can be equipped with a hydraulic tilting function for easy loading of new coils. A telescopic arm aids in feeding the coil into the bending machine. Both the vertical bending machine and the de-coiler are operated via remote control.
The vertical plate bending machine is designed for rolling straight plates or material from coils. It can be equipped with either 3, 4, or 7 rolls, and can be customized to accommodate different plate heights and thicknesses. The rolls are covered with urethane to prevent contamination of the rolled material. The machine is connected to a de-coiler for processing material directly from coils, which can be equipped with a hydraulic tilting function for easy loading of new coils. A telescopic arm aids in feeding the coil into the bending machine. Both the vertical bending machine and the de-coiler are operated via remote control.
Vertical Plate Bending Machine + Plate Track
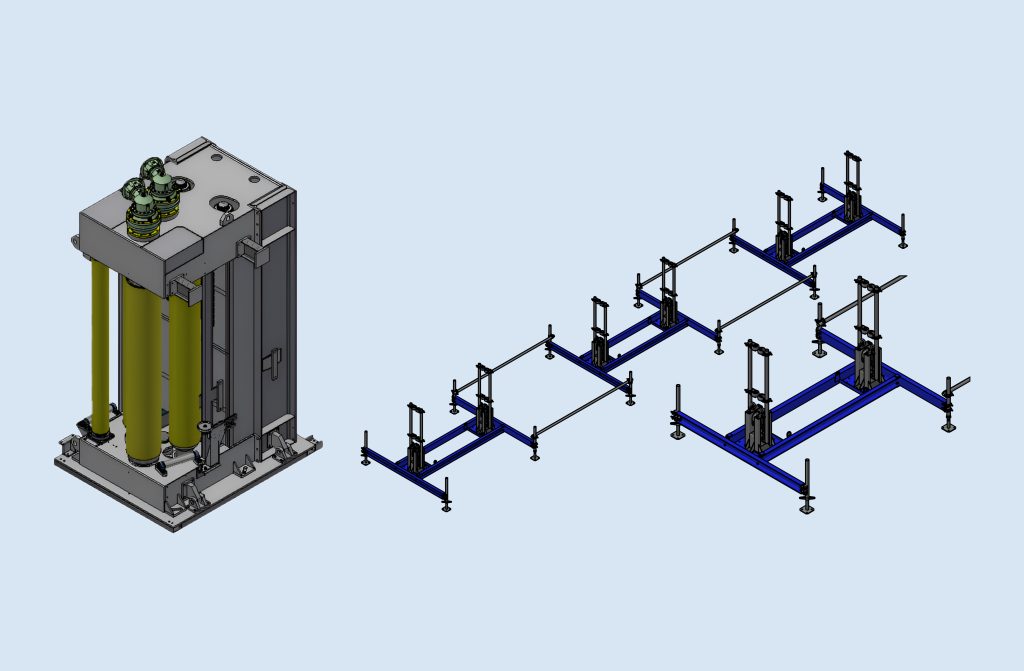
Vertical Plate Bending Machine + Plate Track
Used in conjunction with a vertical bending machine, place flat material onto the plate track and weld the vertical seams. Next, roll the long sheet and feed it into the jacking system.
Used in conjunction with a vertical bending machine, place flat material onto the plate track and weld the vertical seams. Next, roll the long sheet and feed it into the jacking system.
Welding Station
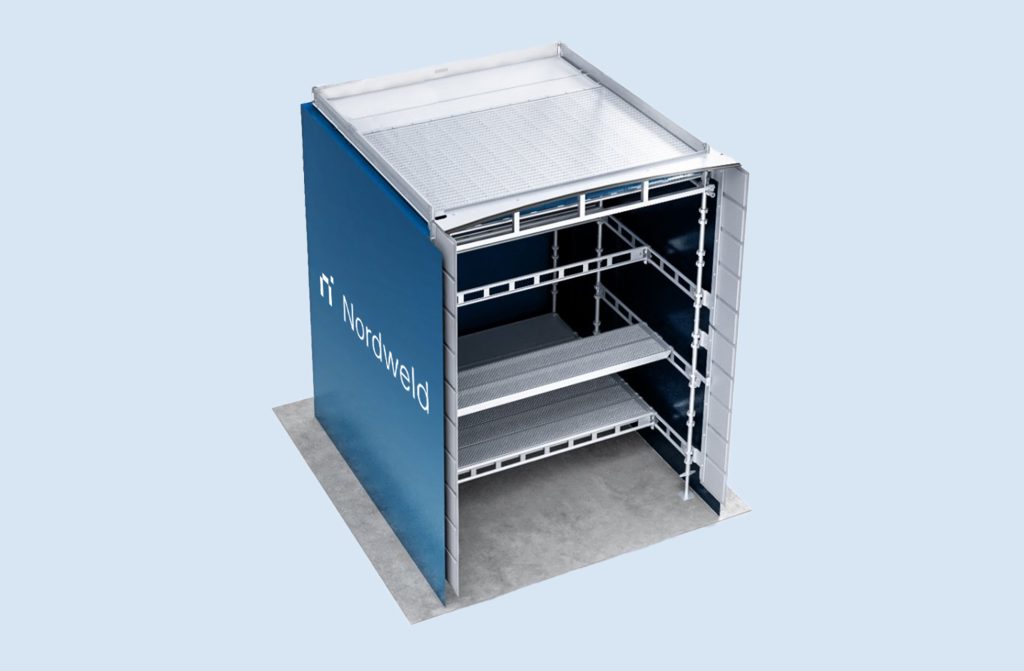
Welding Station
The welding station is constructed using standard aluminum scaffolding components and includes sealing at the top and sides. It is covered with top and side curtains to shield both the operator and the welding equipment from adverse weather conditions while working on the exterior of the tank.
The welding station is constructed using standard aluminum scaffolding components and includes sealing at the top and sides. It is covered with top and side curtains to shield both the operator and the welding equipment from adverse weather conditions while working on the exterior of the tank.
Container
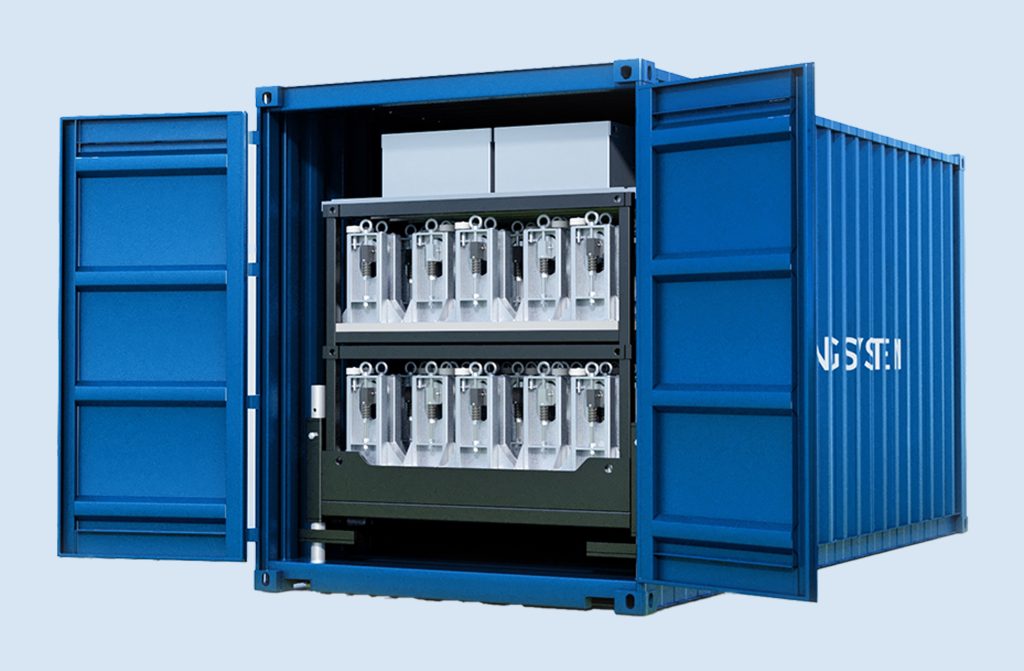
Container
The system is delivered in a 20ft HC shipping container, where it is securely placed in specially designed interior racks. This setup not only makes transport and delivery cost-effective but also ensures the system arrives ready for immediate use. For efficient and safe handling onsite, the transport rack can be easily pulled out of the container, facilitating faster loading and unloading.
The system is delivered in a 20ft HC shipping container, where it is securely placed in specially designed interior racks. This setup not only makes transport and delivery cost-effective but also ensures the system arrives ready for immediate use. For efficient and safe handling onsite, the transport rack can be easily pulled out of the container, facilitating faster loading and unloading.
Internal Scaffolding
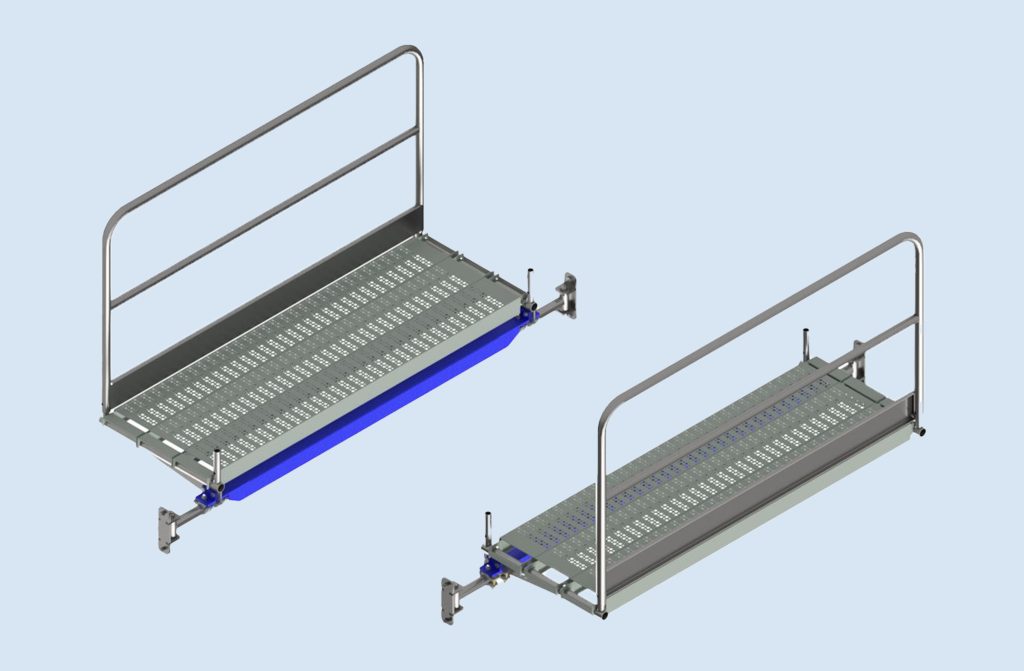
Internal Scaffolding
An internal scaffolding system can be assembled between the jacks to create working platforms inside the tank. This system can be configured in one or two levels and comes equipped with railings. The platforms are constructed from 2050 mm steel planks, with lower-level railings made from 48 mm aluminium pipes and clamps. The upper level includes railing units with a middle bar and kick plates to ensure compliance with safety regulations.
An internal scaffolding system can be assembled between the jacks to create working platforms inside the tank. This system can be configured in one or two levels and comes equipped with railings. The platforms are constructed from 2050 mm steel planks, with lower-level railings made from 48 mm aluminium pipes and clamps. The upper level includes railing units with a middle bar and kick plates to ensure compliance with safety regulations.